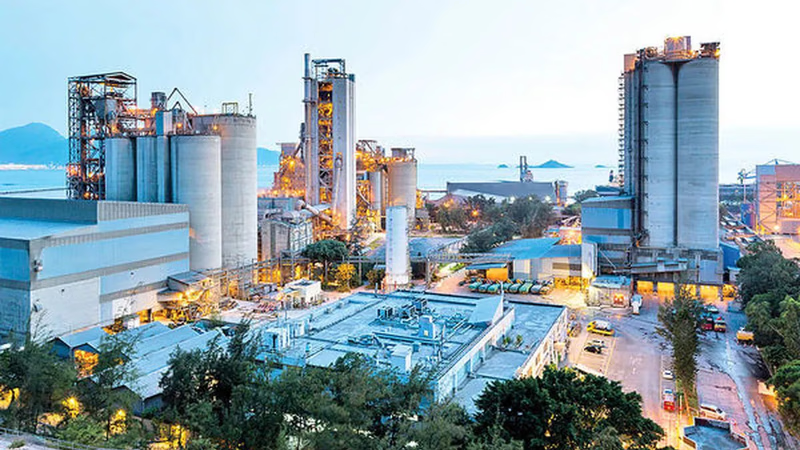
How is the cement trade shaping construction in West Asia?
The cement industry plays a pivotal role in shaping the construction and infrastructure sectors across West Asia and the Middle East. Cement, a key material in building and construction, is highly demanded in the region due to rapid urbanization and large-scale infrastructure projects. The West Asian cement market is both a significant consumer and exporter, with countries in the Middle East exporting cement to global markets, driven by surplus production and competitive pricing. Middle Eastern cement consumption is fueled by increasing construction activities, including residential, commercial, and industrial developments. In addition to cement, related construction materials such as plaster, sand, clay, wood, ceramic tiles, and lime are integral to the regional construction supply chain. The Asian Gypsum Plaster Market is thriving, with large-scale gypsum industries producing boards and plaster products for regional and export needs. Similarly, the demand for sand in West Asia remains robust, with a well-established trade network connecting buyers and sellers across the Middle East and Asia. Timber and raw wood also hold a vital place, with imports and exports ensuring supply for diverse applications, from structural beams to interior finishes.
Innovative advancements like high-tech cement and clinker are reshaping the future of the cement industry globally, with sustainable and performance-enhancing products gaining traction. As demand grows, regional B2B marketplaces and trade platforms are providing verified exporters and importers with tools for business networking, market insights, and supply chain solutions. Platforms like Aritral facilitate direct communication, product listings, and AI-powered marketing to streamline trade operations. With the Middle East emerging as a hub for commodities like cement, glass, bricks, and concrete blocks, the region"s economic vitality continues to attract global attention. The West Asian brick trade, for example, reflects the construction boom, with trends pointing toward increased imports and exports across regional markets. The future of these industries will likely hinge on sustainable practices, technological innovations, and robust trade ecosystems. "
-
Kamran Rafiq 1 months ago
United Arab Emirates COAL AND BUILDING MATERIALS TRADING
HELLO SIR I HAVE CHARCOAL AND BUILDING MATERIALS ALL ITEM\S CONTACT +971521940923`Details
-
شمش آهن و میلگرد 1 months ago
Iran Export of iron billets and rebar and aluminum and urea and sulfur and cement
We at the export and import trade office are capable of supplying iron billets and rebar as well as aluminum and copper billets, and also supplying ce...Details
-
Kemet Export-Import 2 months ago
Egypt Building Materials
Kemet Import & Export owns its own factory in Egypt and is an exclusive agent for major cement and iron and steel factoriesDetails
-
Ali Diabi 2 months ago
Iran Building Stone
I am an exporter of building stones to European and Asian countries.Details
-
Eng. Lotfy Kamel 3 months ago
Egypt Mineral and Industrial Raw Materials
We are a rapidly growing Egyptian company, founded by a group of specialized experts who have great experience in the field of trade, mining, and supp...Details
-
Gogoods 3 months ago
Armenia B2B Company in Armenia
We are proud to offer a wide and diverse range of products including industrial goods, agricultural products, building materials, food items, pet supp...Details
-
Nooshin Khoddami 3 months ago
Iran Iranian Goods
Dorrin company is ready to deliver all the mentioned goods in the shortest time at the best price at the entry points of Asian and Middle Eastern coun...Details
-
Abd Alhakim Bargan Bargan 5 days ago
Libya Cement
Greetings to you. What is required is gray portland cement N42.5 according to American specifications. It must be a nylon bag with a capacity of 50 ki...Details
-
Cihan Ticaret 5 months ago
Turkey Construction materials, hand tools, and generators
“Your Reliable Address for All Construction Needs! ” Complete your projects with confidence using high-quality construction materials, hand tools, and...Details
-
Mohamed Abdelhamed 5 months ago
Egypt Cement
We excel in global quality and competitive prices, which is evident from the analyses and samples that we will send to you.Details
-
Altinhat Diş Ti̇caret 5 days ago
Turkey LEADING SUPPLY COMPANY IN THE CONSTRUCTION AND FOOD SECTOR
CALL US FOR INFORMATION ABOUT QUALITY PRODUCTS AND PRICESDetails
-
Mohammadreza Monfared 5 days ago
Armenia Building Materials
Buying and selling building materialsDetails
-
Hassan 7 months ago
Syria Foam Block
Production of foam blocks in various sizes according to needsDetails
-
Safamarwa Enterprise S 8 months ago
Pakistan Cement
I am exporting cement and bricks since 10 years to Oman and Bahrain.Details
-
Middle East Brick Trade Trends and Market Insights
The brick industry in the Middle East and West Asia is a pivotal part of the region"s construction and trade ecosystem. Bricks, made from materials like clay, sand, and lime, are foundational in construction due to their durability and versatility. The Middle Eastern brick market is witnessing significant growth, fueled by urbanization and infrastructure development. Key types of bricks, including clay bricks, concrete blocks, and ceramic tiles, play a central role in the construction of residential and industrial structures. Notably, trade codes such as 690100 and 690290 govern the import and export of bricks within West Asia. The trade dynamics in the region reveal an evolving marketplace. Verified exporters and importers leverage Middle East trade platforms to facilitate seamless transactions. Demand for bricks, alongside related construction materials like plaster, cement, and rebar, is driven by large-scale infrastructure projects.
Import and export trends show that countries in the Middle East are both major producers and consumers, reflecting a balanced trade relationship. For example, the export of clay-based bricks from countries like Saudi Arabia and the UAE is complemented by imports of specialized ceramic tiles and lightweight concrete blocks. Additionally, the rise of B2B marketplaces in Asia offers enhanced visibility for regional product listings, providing market insights and fostering business networking. Platforms like Aritral enable direct communication and AI-powered marketing to connect suppliers with global buyers. This is particularly crucial for commodities like bricks, which require reliable supply chain solutions to meet project timelines. As the construction boom continues in this region, the brick market is poised for sustained growth, underpinned by robust trade partnerships and technological advancements in manufacturing. "
-
West Asia Cement Industry and Regional Trade Trends
The cement industry plays a pivotal role in shaping the construction and infrastructure sectors across West Asia and the Middle East. Cement, a key material in building and construction, is highly demanded in the region due to rapid urbanization and large-scale infrastructure projects. The West Asian cement market is both a significant consumer and exporter, with countries in the Middle East exporting cement to global markets, driven by surplus production and competitive pricing. Middle Eastern cement consumption is fueled by increasing construction activities, including residential, commercial, and industrial developments. In addition to cement, related construction materials such as plaster, sand, clay, wood, ceramic tiles, and lime are integral to the regional construction supply chain. The Asian Gypsum Plaster Market is thriving, with large-scale gypsum industries producing boards and plaster products for regional and export needs. Similarly, the demand for sand in West Asia remains robust, with a well-established trade network connecting buyers and sellers across the Middle East and Asia. Timber and raw wood also hold a vital place, with imports and exports ensuring supply for diverse applications, from structural beams to interior finishes.
Innovative advancements like high-tech cement and clinker are reshaping the future of the cement industry globally, with sustainable and performance-enhancing products gaining traction. As demand grows, regional B2B marketplaces and trade platforms are providing verified exporters and importers with tools for business networking, market insights, and supply chain solutions. Platforms like Aritral facilitate direct communication, product listings, and AI-powered marketing to streamline trade operations. With the Middle East emerging as a hub for commodities like cement, glass, bricks, and concrete blocks, the region"s economic vitality continues to attract global attention. The West Asian brick trade, for example, reflects the construction boom, with trends pointing toward increased imports and exports across regional markets. The future of these industries will likely hinge on sustainable practices, technological innovations, and robust trade ecosystems. "
-
Exploring the Ceramic Tile Trade in Middle East and Asia
Ceramic tiles, a cornerstone in global construction materials, have seen increasing demand across the Middle East and West Asia due to their durability, aesthetic appeal, and wide application. The Asian ceramic tile market, including HS codes like 690490, 690510, 690790, and 690890, plays a pivotal role in supplying tiles to these regions. Ceramic tiles are used extensively in residential, commercial, and industrial projects, providing benefits such as fire resistance, easy cleaning, and aesthetic versatility. The Middle East trade platform has enabled streamlined buying and selling of ceramic tiles, connecting verified exporters and importers through B2B marketplaces. Industry players leverage these platforms for regional product listings, market insights, and business networking to meet demand efficiently. Countries in West Asia, such as Saudi Arabia, UAE, and Qatar, are major importers of ceramic tiles, driven by booming construction activities. Supply chain solutions in Asia focus on optimizing ceramic tile production and distribution. Notable trends include increasing exports from India and China, which dominate production due to advanced manufacturing facilities and cost-effective pricing.
Additionally, regional trade advertising platforms are promoting ceramic tiles alongside complementary materials like cement, plaster, sand, and glass. The import-export dynamics in the West Asian ceramic tile market reflect broader construction trends, including urbanization and infrastructure development. Verified suppliers and buyers ensure quality and compliance, while competitive pricing remains a key factor in market success. Platforms such as Aritral provide AI-driven tools to simplify trade processes and expand global sales opportunities for ceramic tile manufacturers. By fostering direct communication and profile management, these platforms enhance the efficiency of commodity trade in the Middle East and West Asia.
-
Middle East Clay Market and Trade Dynamics
Clay, a vital construction material, plays a key role in Middle East and West Asian markets, underpinned by its critical applications in ceramics, bricks, and cement production. With demand surging due to expanding infrastructure projects, the Middle East clay market is witnessing robust growth. The region"s verified B2B platforms streamline clay trade by connecting reliable exporters and importers, facilitating cross-border transactions. In West Asia, clay is extensively traded as a raw material for ceramic tiles, a booming industry driven by urbanization. Countries like the UAE and Saudi Arabia are large importers of high-quality clay, while Asian exporters, including India and China, dominate supply channels. These trade dynamics emphasize the importance of supply chain solutions and market insights to navigate challenges like fluctuating prices and transport logistics. Types of clay, such as kaolin and bentonite, cater to diverse applications, including construction, ceramics, and industrial use. Verified exporters and importers leverage platforms listing regional products to target niche demand.
Beyond clay, related materials like plaster, sand, and timber also show synergies in the Middle East market, underpinning construction trends. The popularity of clay-based products, particularly bricks and ceramic tiles, has significantly shaped the construction industry in West Asia. Key benefits of clay include its durability, thermal insulation, and eco-friendly properties. However, challenges like environmental impact and sourcing quality clay remain critical concerns. Aritral, an AI-driven B2B platform, simplifies commodity trade by offering product listing, verified contact networks, and AI-powered marketing. Businesses in the clay trade can leverage Aritral to tap into evolving market demands and enhance their cross-border operations. "
-
Global Trade Insights: Lightweight Concrete Block Market in Asia and Middle East
The Middle East and West Asia are pivotal regions in the global trade of construction materials, including concrete blocks. Lightweight concrete blocks, such as AAC (autoclaved aerated concrete) and ACB (autoclaved concrete blocks), are gaining prominence due to their eco-friendly properties and structural efficiency. Regional demand for these materials has surged, driven by urbanization, infrastructure growth, and green building initiatives. Verified B2B marketplaces in Asia are instrumental in connecting importers and exporters, ensuring compliance with international standards like HS codes 681011, 681019, and 690100. These platforms enable direct communication, fostering trust and transparency in transactions. Market trends indicate an increase in lightweight concrete block exports from West Asia, particularly to South Asia and East Africa, where demand for durable yet lightweight construction materials remains high. Beyond concrete blocks, related commodities such as plaster, sand, timber, and lime play significant roles in regional supply chains. The Asian gypsum plaster market, for instance, has seen growth due to its application in modern construction.
Similarly, sand trade in West Asia is evolving, with verified suppliers meeting stringent quality standards. Timber and glass, essential for construction, are also actively traded across regional markets. The marketing and export of lightweight concrete blocks and related materials require robust supply chain solutions, advanced trade advertising platforms, and reliable insights into market dynamics. Aritral, an AI-driven B2B trade platform, simplifies global sales assistance, profile management, and product listings for verified exporters and importers in these sectors, ensuring streamlined operations in the competitive Middle Eastern and Asian markets.
-
Glass Trade Dynamics in West Asia and Middle East
The glass industry in West Asia and the Middle East is witnessing significant growth, driven by increasing demand in construction, packaging, and automotive sectors. Glass, along with other building materials like plaster, sand, wood, lime, and cement, plays a pivotal role in shaping regional infrastructure projects. As urbanization accelerates, particularly in developing economies, verified exporters and importers are leveraging trade platforms and B2B marketplaces to streamline supply chains and meet growing demands. The Asian glass market, which includes products such as tempered, laminated, and float glass, is becoming a key source for Middle Eastern buyers. Categories like 700100 (glass cullet), 700231 (glass in sheets), and 700521 (glassware) are central to regional trade. Verified suppliers on platforms like Aritral facilitate direct communication and market insights for import/export activities, ensuring transparency and efficiency. Glass trade and marketing in the Middle East also intersect with other construction materials, highlighting the importance of supply chain solutions to meet large-scale project requirements. Beyond glass, materials like rebar and beams, bricks, ceramic tiles, and concrete blocks are essential to regional construction trends, with a growing focus on lightweight and eco-friendly products.
Efforts to expand trade networks and enhance business networking opportunities are enabling smoother transactions between buyers and sellers. For instance, connecting with Asian glass suppliers through verified B2B platforms fosters reliability and trust in cross-border trade. Market insights and advertising platforms further aid businesses in making informed decisions, while regional product listings improve visibility and accessibility. Aritral, an AI-powered trade platform, simplifies the buying and selling process for commodities like glass, offering tools like profile management, global sales assistance, and AI-driven marketing solutions. With its focus on verified listings and direct communication, Aritral is helping businesses capitalize on the economic potential of Middle Eastern and West Asian trade corridors.
-
Plaster in Construction Trade: Trends in West Asia and Middle East
Plaster, a cornerstone material in the construction industry, plays a pivotal role in West Asia’s growing infrastructure and trade ecosystem. Derived primarily from gypsum, plaster is widely used as a building material, with applications ranging from wall coatings to decorative finishes. The Asian Gypsum Plaster Market is witnessing significant growth due to rising construction activities, particularly in the Middle East, where urbanization and infrastructure projects are booming. Plaster of Paris (POP), a key derivative of gypsum, is highly sought after in West Asia for its quick-setting properties and versatility in architectural moldings and surface finishing. West Asia"s trade platforms, such as B2B marketplaces, are driving the expansion of verified plaster suppliers and import/export partnerships. These platforms facilitate the listing of regional products, including plaster, sand, lime, and other construction materials like bricks, cement, and ceramic tiles. The integration of AI-powered solutions on trade platforms streamlines supply chain management and connects verified exporters and importers, enhancing market transparency. The demand for high-quality plaster has also spurred the development of gypsum board and plaster manufacturing industries in Asia.
With increasing preferences for lightweight and sustainable construction materials, gypsum plaster is becoming a preferred choice over traditional materials like clay and concrete blocks. Additionally, the import and export of other complementary materials, such as sand, lime, and timber, are crucial for the construction sector in the Middle East and West Asia. As a trade advertising platform, tools like Aritral provide valuable market insights, promoting business networking and facilitating cross-border commerce. By connecting regional traders and providing verified supplier profiles, these platforms are reshaping the dynamics of the construction materials trade in Asia and the Middle East. "
-
Rebar and Beam Trade in West Asia and Middle East
The construction materials market in the Middle East and West Asia is undergoing significant transformation, driven by innovative B2B platforms and the evolving dynamics of supply chains. Among the standout materials are rebar and beam, which form the backbone of structural steel trade in the region. The demand for these materials is increasing due to rising infrastructure projects, urbanization, and government-led construction initiatives. Verified exporters and importers across the Middle East and Asia are leveraging platforms to streamline the trade of rebar and beams, ensuring compliance and quality. Plaster, another key material, is playing a transformative role in West Asia"s construction sector. Gypsum-based plaster, including Plaster of Paris, has witnessed a surge in demand due to its application in modern interiors and energy-efficient constructions. Verified suppliers and market insights are critical for traders to navigate this growing sector. The sand trade in the Middle East is equally dynamic, with imports and exports driven by high demand for construction-grade sand.
Similarly, the wood and timber market has shown robust activity, as raw materials continue to flow into developing urban areas. Lime, a staple in construction, is shaping trade trends with its pivotal role in cement production and soil stabilization. Other materials like glass, bricks, ceramic tiles, and lightweight concrete blocks are also gaining prominence, supported by regional B2B marketplaces that facilitate trade transparency and efficiency. The structural steel export market is particularly noteworthy, as rebar and beams dominate imports and exports. West Asia"s verified B2B networks ensure seamless transactions and market insights, enabling businesses to meet regional demands. Aritral, an AI-driven trade platform, is optimizing supply chains and connecting global entities through product listing, direct communication, and AI-powered marketing, fostering a more efficient trade environment for commodities like structural steel, plaster, and other construction essentials.
-
Insights into the Sand Trade in West Asia and Middle East
Sand, a vital construction material, plays a central role in the trade dynamics of West Asia and the Middle East. Its applications span across infrastructure development, from concrete production to manufacturing glass, bricks, and ceramic tiles. The annual global consumption of sand is estimated to be 50 billion tons, driven heavily by the construction industry. In the Middle East, where rapid urbanization and infrastructure projects are booming, sand is a highly demanded commodity. This demand has led to substantial import and export activities, with verified buyers and sellers leveraging B2B marketplaces to streamline transactions. The Asian sand market is particularly robust, with West Asia acting as a critical trade hub. Importers from the Middle East often rely on regional trade platforms to connect with suppliers offering various types of sand, including silica, river sand, and fine aggregates. Verified exporters ensure quality while addressing logistical challenges through advanced supply chain solutions.
Platforms like Aritral assist stakeholders by providing market insights, direct communication tools, and regional product listings, making transactions efficient and transparent. Sand’s significance extends beyond construction. It is used in glass production, cement manufacturing, and as a filler in plaster and paints, further solidifying its importance in the commodity trade. With increasing environmental concerns about sand mining, the industry is exploring sustainable sourcing and innovative trade solutions. Verified B2B platforms are critical in ensuring compliance with regulations and fostering collaboration among sand buyers and sellers. West Asia’s sand trade reflects broader construction material trends, including plaster, lime, ceramic tiles, and concrete blocks. These materials collectively support the region"s infrastructure evolution, driven by urban expansion and modernization efforts. By leveraging advanced trade advertising platforms and business networking tools, regional stakeholders continue to optimize their supply chains for sustainable growth. "
-
Lime Trade in West Asia: Market Trends and Insights
Lime, a versatile construction material, plays a pivotal role in West Asia"s growing building sector. As demand for infrastructure development surges in the region, lime has become a critical commodity, particularly for industries like plaster, cement, and ceramics. West Asian countries, with their abundant mineral deposits, are emerging as key suppliers and exporters of high-quality lime. Verified exporters and importers facilitated by B2B marketplaces are streamlining trade dynamics, ensuring quality and transparency across the supply chain. The lime trade in West Asia thrives on its integration with other building materials such as sand, bricks, and concrete blocks, which are essential for the construction boom in the Middle East. Platforms like Aritral enable businesses to leverage regional product listings, market insights, and direct communication tools for efficient sourcing and sales. Verified suppliers ensure that lime meets industry standards, strengthening confidence among buyers globally. West Asia"s lime market is also shaped by its proximity to other major markets in Asia, enabling smooth import/export processes.
Countries like the UAE and Saudi Arabia lead in lime consumption, driven by urbanization and large-scale construction projects. The supply chain solutions offered by regional trade platforms further enhance the efficiency of managing lime-related transactions, from marketing to distribution. Besides lime, the region"s focus on complementary construction materials — plaster, sand, wood, glass, rebar, and beams — highlights the interconnected nature of the commodity trade. By analyzing market trends and leveraging AI-driven tools, businesses in West Asia can maximize their reach and profitability. The lime trade"s integration with verified B2B platforms is fostering sustainable and transparent trade practices, ensuring continued growth in the Middle Eastern construction industry.
-
Middle East Paint Trade Insights: Construction Paint Market Trends
The construction materials trade in West Asia and the Middle East is experiencing dynamic growth, particularly in the paint sector, driven by regional infrastructure projects and urbanization. The Asian construction paints market is vibrant, offering a vast array of choices, including all types of colors tailored for diverse construction needs. Verified exporters and importers play a pivotal role in ensuring quality and compliance in the import/export of building paints. This trade is facilitated by B2B marketplaces, which provide regional product listings and market insights essential for navigating the sector’s complexities. The Middle East’s burgeoning construction industry has amplified demand for building paints, ranging from standard to specialized formulations. Key players in the industry include the world’s largest manufacturers and exporters, who leverage supply chain solutions to meet regional needs. Marketing and trading of construction paints in the Middle East are increasingly tied to digital platforms like Aritral, which simplify trade through AI-driven product listings, global sales assistance, and direct communication tools. In addition to paints, construction materials like plaster, sand, wood and timber, lime, glass, rebar and beam, brick, cement, ceramic tiles, clay, and concrete blocks are critical for West Asia’s infrastructure growth.
For instance, the Asian Gypsum Plaster Market supports the plaster trade, while verified suppliers dominate the sand import/export sector. Similarly, timber and lime trade trends showcase their importance across supply chains in the construction sector. Glass, rebar, bricks, and cement are shaping construction dynamics through robust trade networks powered by platforms offering efficient marketing and export solutions. The paint sector, however, remains a standout due to its versatility and role in architectural aesthetics and durability. Investigating supply and demand trends in West Asian countries reveals significant opportunities for exporters, particularly in lightweight concrete blocks and ceramic tiles, which complement the building paint sector. Aritral’s AI-powered platform ensures smooth navigation of these trade dynamics, aligning with global business growth.
-
Dynamic Trade Trends in Wood and Construction Materials in West Asia
The construction materials trade in West Asia and the Middle East is witnessing a dynamic shift, fueled by increasing demand for essential commodities like wood, timber, plaster, sand, lime, and glass. Among them, the wood and timber market has become a cornerstone of construction and furniture manufacturing. The raw wood trade, particularly encompassing HS codes 440110 to 440500, is thriving due to growing urbanization and infrastructure projects in countries like the UAE, Saudi Arabia, and Turkey. Verified exporters and importers, leveraging B2B platforms, are streamlining supply chains to meet the demand for high-quality timber products. Plaster, specifically gypsum-based products like Plaster of Paris, is another critical material shaping West Asia"s construction industry. Its lightweight and cost-effective properties make it an essential component in infrastructure development. Similarly, sand and lime play irreplaceable roles in construction, with verified suppliers ensuring steady availability for projects ranging from residential complexes to megastructures. Structural materials like rebar, beams, bricks, cement, and concrete blocks are gaining traction as the backbone of West Asia’s booming construction sector.
Lightweight concrete blocks, in particular, are becoming a sustainable choice for modern building designs. The ceramic tile market is also expanding, with increasing exports to European and Asian markets reflecting its aesthetic and functional appeal. Glass, another key commodity, is undergoing transformation with the aid of B2B trade platforms that connect regional suppliers with global buyers. Verified listings are ensuring transparency and efficiency in the market. Aritral, an AI-driven B2B platform, simplifies the trading process for these commodities, offering product listings, direct communication, and AI-powered marketing solutions. By facilitating connections between verified suppliers and buyers, Aritral enhances market transparency and efficiency across the Middle East and West Asia. "
-
Future of cement industry
The cement industry is undergoing significant transformation aimed at reducing environmental impact and enhancing sustainability. Key initiatives include the development of alternative cementitious materials, such as geopolymers and calcium sulfoaluminate cements, which produce lower carbon emissions than traditional Portland cement. The sector is increasingly focusing on energy efficiency, cleaner production technologies, and the use of waste materials as alternative raw materials or fuels. This trend not only aids in waste reduction but also promotes resource conservation. As urbanization accelerates, particularly in emerging economies, the demand for cement remains strong due to ongoing infrastructure development needs. The industry is also adapting to prefabrication and modular construction methods, which enhance efficiency and reduce material waste. Furthermore, advancements in technology are expected to revolutionize cement manufacturing through innovations like carbon capture and utilization/storage (CCU/CCS) and novel kiln designs. Digitalization and automation are being embraced to optimize production processes, improve quality control, and enhance operational efficiency through data analytics and machine learning. These changes reflect a broader shift towards sustainability and efficiency within the industry as it prepares for future challenges related to population growth, environmental concerns, and technological advancements.
-
What changes will occur in the cement industry in the future?
The cement industry is set to undergo significant transformations focused on sustainability and efficiency. Key trends include the adoption of alternative cementitious materials, such as fly ash and slag, which can reduce carbon emissions and promote waste utilization. Innovations in roller mill design will enhance grinding performance while minimizing energy consumption. The integration of digital technologies, including data analytics and artificial intelligence, will optimize production processes and improve product quality. Automation will play a crucial role, potentially reducing the need for manual labor and shifting workforce requirements towards information engineers and technical specialists. Additionally, advancements in preheating technologies and heat recovery systems will further enhance energy efficiency in clinker production. The industry is also expected to embrace circular economy principles by utilizing industrial by-products as alternative raw materials. As construction practices evolve with prefabrication and 3D printing, cement manufacturers must adapt their products accordingly. Overall, these changes aim to create a more sustainable, efficient, and technologically advanced cement industry.
-
Precautions in cement storage
Proper cement storage is crucial for maintaining its quality and integrity. Cement must be kept in a dry, well-ventilated environment to prevent moisture absorption, which can lead to clumping and reduced performance. It is essential to store cement off the ground on pallets or racks, ensuring that bags are stacked to allow air circulation and minimize contact with walls or floors. Extreme temperatures should be avoided; thus, a temperature-controlled environment is recommended. Implementing a FIFO (First In, First Out) system helps ensure older stocks are used first, maintaining freshness and quality. Additionally, proper inventory management and labeling are vital for tracking stock effectively. Cement should be stored away from contaminants like chemicals or fuels that could affect its setting properties. Regular inspections for moisture or damage are necessary to address any issues promptly.
Security measures should also be in place to restrict access to authorized personnel only, preventing theft or tampering. Training staff on safe handling practices and the use of personal protective equipment (PPE) is essential for health safety during cement storage operations.
-
Loading cement for consumption and cement warehouse
Loading cement for consumption and managing a cement warehouse involves receiving bulk or bagged cement from manufacturers and storing it for distribution. Bulk cement is transported in specialized vehicles, while bagged cement is packaged in standard bags. The loading process utilizes pneumatic or mechanical systems to transfer cement from storage to transportation vehicles. Warehouse design must prioritize storage capacity, accessibility, ventilation, and safety regulations. Efficient logistics planning is essential for optimizing delivery routes and minimizing costs. Orders can be received through various channels, and the loading process may involve conveyor belts or forklifts. Proper cleanliness of the warehouse environment is crucial to maintain quality during storage and loading. Cement can be provided in bulk or bagged forms, with specific labeling requirements for each type.
Inventory management ensures timely availability of cement by tracking shipments and implementing a first-in-first-out system. Quality control measures are necessary to meet standards and prevent contamination.
-
Where is the first destination of Middle East cement exports?
The Middle East, particularly the GCC countries, is a significant player in the global cement market, with India being the top destination for cement exports. In the first five months of this year alone, over 5. 8 million tons of cement valued at nearly $128 million were exported from the region. The demand for cement in the GCC nations stems from extensive construction and infrastructure projects. North African countries like Egypt and Algeria also import substantial amounts of cement due to their ongoing development needs. East African nations such as Kenya and Tanzania are similarly increasing their imports as urbanization accelerates. Challenges facing the industry include supply chain disruptions, increased production costs, and transportation issues exacerbated by the COVID-19 pandemic. Other notable importers include Iraq, Kuwait, and Afghanistan, which rank among the highest in terms of import value.
The UAE and Saudi Arabia are leading exporters within the region, bolstered by their robust cement industries. Oman is also expanding its production capacity to enhance export capabilities. Additionally, Turkey and Iran contribute significantly to regional exports due to their established cement sectors.
-
What is cement?
Cement is a crucial building material that binds sand particles, forming a solid structure essential in construction. It is produced by heating calcareous materials, clay, and silica at high temperatures, resulting in a durable product that hardens when mixed with water. The most common type is Ordinary Portland Cement (OPC), used for general construction. Variants like White Cement and Rapid Hardening Cement cater to specific needs, such as aesthetics and quick strength development. The production process involves extracting raw materials, crushing them into powder, and heating them in a kiln to create clinker, which is then ground into cement powder. Cement"s chemical reaction with water during hydration leads to hardening, providing strength to various structures including buildings, bridges, and roads. However, cement production has environmental impacts due to greenhouse gas emissions. Efforts are underway to mitigate these effects through alternative materials and energy-efficient technologies.
Understanding the properties and applications of cement is vital for stakeholders in the Middle East trade platform and B2B marketplace Asia. "
-
The world's top cement producers
LafargeHolcim leads the global cement industry, operating in over 70 countries. Other major players include China"s CNBM and Anhui Conch Cement, both known for their extensive production capabilities and innovation. HeidelbergCement from Germany and Cemex from Mexico also rank among the top producers, emphasizing sustainability and customer-centric solutions. In 2019, China maintained its dominance with a production of 2200 million tons, followed by India at 320 million tons and Vietnam at 95 million tons. The United States ranked fourth with 89 million tons, while Egypt and Indonesia produced 76 million and 74 million tons respectively. Iran"s production increased to 60 million tons, elevating it to seventh place globally as Turkey"s output fell significantly. Other notable producers include Russia, Brazil, South Korea, and Japan. The cement market is characterized by a mix of established companies focusing on innovation and sustainability while navigating fluctuating production rates across different regions. "
-
What are the types of cement and what are they used for?
Various types of cement serve distinct purposes in construction, each tailored to meet specific strength and durability requirements. Ordinary Portland Cement (OPC) is the most common, suitable for general construction like residential buildings and pavements. Portland Pozzolana Cement (PPC) enhances workability and durability, ideal for hydraulic structures and marine environments. Other types include rapid hardening cement for expedited projects, sulphate resistant cement for sulfate-rich environments, and blended cements that improve sustainability by incorporating industrial by-products. Each type of cement is formulated to address unique environmental conditions and project demands, ensuring optimal performance in diverse applications. The choice of cement affects workability, setting time, and overall structural integrity. As sustainability becomes a priority in construction, blended cements are gaining traction due to their reduced environmental impact.
-
High Tech Cement and Clinker
High-tech cement and clinker represent advanced materials in construction, offering enhanced performance, durability, and sustainability. Innovations include blended cements that incorporate supplementary cementitious materials (SCMs) like fly ash and slag to improve strength and reduce environmental impact. Low-carbon cements aim to lower CO2 emissions through alternative binders or modified formulations. High-tech clinker production focuses on reducing environmental effects by utilizing novel binders and integrating carbon capture technologies. These advancements are essential for achieving sustainable construction practices, balancing performance with economic viability. The industry is evolving towards producing innovative cement-based products such as lightweight and self-healing concrete, driven by technological progress. However, demographic changes and overcapacity in the cement sector may lead to a significant decline in demand for traditional cement by mid-century. As developing countries modernize their infrastructure, some cement plants may become obsolete or need to adapt their operations.