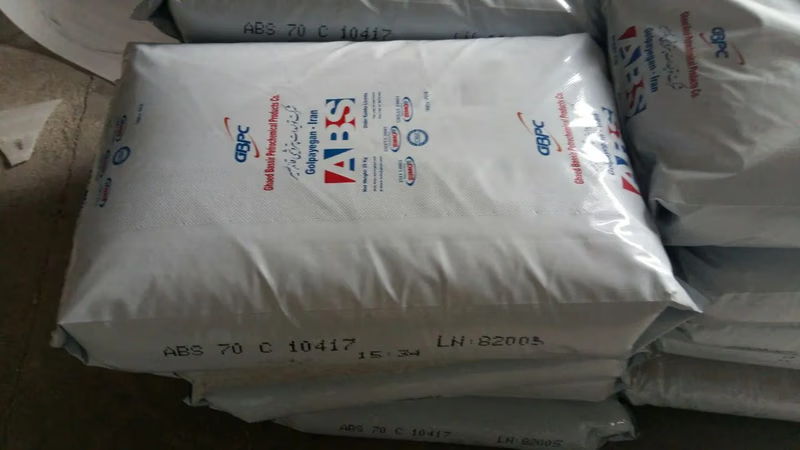
How are B2B platforms shaping the ABS market in the Middle East?
Acrylonitrile Butadiene Styrene (ABS) is a resilient thermoplastic polymer widely used in industries such as automotive, electronics, and construction. In the Middle East, the ABS market is experiencing notable growth due to increasing demand across these sectors. This expansion is supported by the region"s robust petrochemical industry, which ensures a steady supply of essential feedstocks such as butadiene, acrylonitrile, and styrene. Key West Asian players leverage their proximity to raw material sources, including ethylene, polypropylene, and styrene butadiene rubber, to strengthen supply chains and meet regional and international demand. B2B trade platforms, such as Aritral, play a pivotal role in enhancing ABS trade dynamics in West Asia. These platforms enable verified exporters and importers to connect, ensuring transparency and reliability in trade. Regional product listings and market insights on commodity trade further help businesses make informed decisions. The West Asian ABS plastic market benefits from these tools, driving both local and international trade.
ABS polymer is especially favored in plastic injection molding, where its high impact resistance, glossy finish, and thermal stability are critical for creating durable products. However, challenges such as fluctuating raw material prices and competition from alternative resins like nylon and polybutadiene impact the market. As the broader petrochemical sector in the Middle East, including butane and propane markets, continues to expand, opportunities for ABS production and trade are set to increase. Verified B2B supply chain platforms are vital for navigating these dynamics, fostering connections, and driving growth in global ABS trade. Aritral simplifies these processes with its AI-driven tools, enabling seamless trade of ABS and other petrochemical commodities. "
-
Hassas Plastik San Ve Tic. A.S. Bursa Turkey 1 weeks ago
Turkey ABS ER400, ABS MATT
We are acquiring ABS ER400 - ABS super matte raw material.Details
-
Ravansazansanat 4 days ago
Iran ravansazan
Types of engine oils and petroleum derivativesDetails
-
Petro Kimia Alfa 1 weeks ago
Turkey Petrochemical Products
Exporter of petrochemical products from IranDetails
-
Aalam Alkimawiyat 7 months ago
Yemen Aalam Alkimawiyat
Aalam Alkimawiyat for medical and laboratory supplies in Sana'a, Yemen offers you a wide range of high-quality chemical and medical products to meet y...Details
-
Iran Jae Jahan Nama Asadi Trading Compani بازرگانی جام جهان نما اسدی
I am a supplier of foos such as Deinks and Juices , Carbonated drinck , and without gas , sparkling water and mineral water all kinds of dry fruits Sa...Details
-
Ali 2 weeks ago
Lebanon n_methylformamide (NMF) CAS.123-39-7
n_methylformamide (NMF) CAS.123-39-7 must bepureDetails
-
Shams International Trading Company 1 weeks ago
Iran Import and export of all kinds of commercial goods
Ready to cooperate in the field of international trade with all countries allowed to tradeDetails
-
مخازن الجمهورية للكيماويات والوسائل العلمية والتعليمية 15 months ago
Yemen Chemicals, Medical Supplies, and Educational Tools
*All available chemicals, medical supplies, and educational and industrial tools for detergents and cosmetics, as well as materials for scientific res...Details
-
Three Points 2 weeks ago
Egypt الحاصيلات الزراعية
Three Points Consultants is the packaging industry’s leading consulting partner. As management consultants, we’ve been fully focused on the packaging...Details
-
Arbenco Petrochemical Company 1 weeks ago
Bahrain I have 50 thousand tons of methanol. Do you buy or do I have a customer for them?
For sale: 50 thousand barrels of methanol, phone number: 0097339211616Details
-
Acrylonitrile Butadiene Styrene Trade in West Asia
Acrylonitrile Butadiene Styrene (ABS) is a resilient thermoplastic polymer widely used in industries such as automotive, electronics, and construction. In the Middle East, the ABS market is experiencing notable growth due to increasing demand across these sectors. This expansion is supported by the region"s robust petrochemical industry, which ensures a steady supply of essential feedstocks such as butadiene, acrylonitrile, and styrene. Key West Asian players leverage their proximity to raw material sources, including ethylene, polypropylene, and styrene butadiene rubber, to strengthen supply chains and meet regional and international demand. B2B trade platforms, such as Aritral, play a pivotal role in enhancing ABS trade dynamics in West Asia. These platforms enable verified exporters and importers to connect, ensuring transparency and reliability in trade. Regional product listings and market insights on commodity trade further help businesses make informed decisions. The West Asian ABS plastic market benefits from these tools, driving both local and international trade.
ABS polymer is especially favored in plastic injection molding, where its high impact resistance, glossy finish, and thermal stability are critical for creating durable products. However, challenges such as fluctuating raw material prices and competition from alternative resins like nylon and polybutadiene impact the market. As the broader petrochemical sector in the Middle East, including butane and propane markets, continues to expand, opportunities for ABS production and trade are set to increase. Verified B2B supply chain platforms are vital for navigating these dynamics, fostering connections, and driving growth in global ABS trade. Aritral simplifies these processes with its AI-driven tools, enabling seamless trade of ABS and other petrochemical commodities. "
-
Exploring Butane and Propane Trade Dynamics in Asia
Butane and propane, two liquefied petroleum gases (LPG), are pivotal commodities in the Middle East and West Asia"s petrochemical trade landscape. These hydrocarbons play a significant role in fueling industrial processes, energy production, and chemical manufacturing. As demand surges in Asia, particularly for reliable energy sources and petrochemical feedstocks, butane and propane trade dynamics have evolved to become more interconnected across regions. Verified exporters and importers utilize B2B marketplaces and trade platforms to streamline supply chains and ensure quality standards. In the Middle East, both butane and propane are by-products of extensive oil and gas refining processes, making the region a leading supply hub. As West Asia boosts its import-export capabilities, these commodities are increasingly transported to energy-hungry Asian markets. B2B platforms such as regional trade advertising platforms and networking solutions facilitate smoother transactions and more transparent business operations, allowing suppliers to connect directly with buyers seeking bulk LPG solutions. The petrochemical derivatives of butane and propane, including ethylene and polypropylene, further underscore their economic importance.
Ethylene serves as a cornerstone for producing polyethylene and specialty resins, while polypropylene has witnessed soaring demand across sectors such as packaging and automotive manufacturing. Insights into styrene butadiene rubber (SBR) and acrylonitrile butadiene styrene (ABS) highlight their relevance in industrial applications, reinforcing the value of verified B2B platforms in shaping trade dynamics for these derivatives across West Asia and the Middle East. Aritral, an AI-driven B2B platform, simplifies international trade by offering AI-powered marketing, direct communication tools, and verified product listings. Such platforms are critical for connecting supply chains in the butane and propane markets, ensuring efficient trade solutions and fostering regional growth. "
-
Ethylene Trade in the Middle East: Petrochemical Opportunities
Ethylene, a vital petrochemical feedstock, is the cornerstone of several industrial applications, including the production of Polypropylene, Polybutadiene, Styrene Butadiene Rubber (SBR), Acrylonitrile Butadiene Styrene (ABS), Nylon, and various resins. In the Middle East, particularly West Asia, ethylene production and consumption are central to the region"s thriving petrochemical industry. The Persian Gulf countries are among the world’s largest producers and exporters of ethylene due to abundant natural gas resources, which serve as a key raw material for its production. On platforms such as Aritral, businesses can buy and sell ethylene, enabling verified exporters and importers to connect seamlessly. As an AI-driven B2B marketplace, it provides supply chain solutions, market insights, and verified product listings tailored to the unique trade dynamics of the Middle East. Ethylene trade in West Asia benefits from robust commodity markets, competitive pricing, and strategic geographic positioning that facilitates global exports. Polypropylene, another significant derivative of ethylene, sees high demand in Southwest Asian markets. Middle Eastern suppliers dominate this segment, exporting to both regional and global markets.
Similarly, Polybutadiene and Styrene Butadiene Rubber (SBR) are integral to the automotive and industrial sectors, with production concentrated in the Middle East. Resins such as polyester, phenolic, silicone, and epoxy, alongside Nylon and LPG derivatives like Butane and Propane, are essential commodities traded across the Middle East and Asia. These products align with the region’s emphasis on petrochemical exports, supported by trade platforms that streamline buyer-seller interactions and provide real-time market trends. Aritral simplifies this ecosystem by offering AI-powered marketing and direct communication tools, ensuring efficient transactions across borders. Businesses seeking to leverage Middle Eastern petrochemical markets can access specialized insights and connect with verified partners efficiently. "
-
Nylon Trade in Middle East & West Asia: Insights, Trends, and Growth
Nylon, a versatile polyamide polymer, has become a cornerstone of global trade, particularly in the Middle East and West Asia. The region"s robust petrochemical infrastructure, driven by abundant resources like ethylene, butane, and propane, provides a solid foundation for nylon production and distribution. Ethylene, a critical feedstock for nylon, plays a pivotal role in shaping trade dynamics in West Asia, linking upstream petrochemical capabilities with downstream industrial applications. Verified B2B marketplaces in Asia are instrumental in facilitating this trade, connecting suppliers with buyers and ensuring transparency across supply chains. Polyamide polymers, including nylon, see significant demand across industries like textiles, automotive, and industrial components. The Middle East nylon market has experienced steady growth, supported by regional product listings and trade advertising platforms that promote buying and selling in West Asian countries. Insights from verified exporters and importers reveal that nylon enjoys high demand due to its durability, versatility, and lightweight properties. Trade dynamics are further influenced by polypropylene and styrene butadiene rubber (SBR) markets, which complement nylon applications in textiles and industrial sectors.
Resins such as acrylonitrile butadiene styrene (ABS) and polybutadiene rubber also play crucial roles in regional supply chains, meeting diverse industrial needs. Middle East trade platforms facilitate these interactions, leveraging AI-driven tools for market insights and supply chain solutions in Asia. Aritral, an AI-powered B2B platform, simplifies the trade of nylon and other polyamide polymers via services like global sales assistance, product listings, and AI-powered marketing. By connecting verified exporters and importers, Aritral ensures seamless trade operations in the nylon market and beyond, contributing to the growing prominence of West Asia in global trade. "
-
Polybutadiene Rubber Market Insights in Middle East & Asia
Polybutadiene, a high-demand synthetic rubber, plays a pivotal role in the petrochemical trade dynamics of the Middle East and West Asia. As one of the largest producers of butadiene rubber, the region benefits from abundant feedstocks like butane and propane, crucial for polybutadiene production. This advantage positions the Middle East as a competitive supplier of Polybutadiene Rubber (PBR) to global markets. The PBR market in West Asia is driven by its use in tire manufacturing, industrial goods, and plastics, with applications extending to Styrene Butadiene Rubber (SBR) and Acrylonitrile Butadiene Styrene (ABS) production. Given its chemical properties like high wear resistance and low-temperature flexibility, Polybutadiene continues to command strong demand in regional and global industries. Verified B2B marketplaces in Asia facilitate the trade of PBR by connecting regional exporters with global importers. These platforms also offer market insights, enabling stakeholders to track Polybutadiene Rubber prices, which vary based on feedstock costs, production rates, and regional demand. Additionally, innovations in supply chain solutions have streamlined the export of PBR, making West Asia a central hub for petrochemical trade.
In the broader petrochemical spectrum, ethylene and polypropylene also significantly impact West Asia"s trade. Ethylene serves as a key precursor in producing PBR and other derivatives, while polypropylene’s versatility supports its soaring demand in Asia. These commodities, alongside polybutadiene, highlight the region’s growing importance in global trade. Business networking platforms like Aritral simplify these trade dynamics by offering verified regional product listings, AI-powered marketing, and connecting exporters and importers. As the Middle East strengthens its position as a petrochemical powerhouse, Polybutadiene and associated products remain at the forefront of the region"s trade growth.
-
Polypropylene Trade Dynamics in Middle East and Asia
Polypropylene, a versatile thermoplastic polymer, plays a pivotal role in the global petrochemical industry, particularly in West Asia and the Middle East. As one of the most widely used plastics, it is produced from propylene, a by-product of ethylene production. The Middle East stands as a key hub for polypropylene manufacturing, with countries like Saudi Arabia, Qatar, and the UAE leading production due to their abundant petrochemical resources. These producers leverage advanced refinery systems and access to raw materials like butane and propane, essential for propylene synthesis. Polypropylene is used across diverse industries, including packaging, automotive, textiles, and consumer goods. Its demand in the Asian market is soaring due to the rapid industrial growth and infrastructural developments in countries like India and China. Verified exporters and importers in these regions rely heavily on B2B marketplaces for efficient supply chain solutions and trade networking. Middle Eastern polypropylene suppliers capitalize on this surge by connecting through regional product listings and trade advertising platforms tailored for commodity trade.
The polypropylene market in West Asia is bolstered by its proximity to major ethylene and polybutadiene production centers. Ethylene, the backbone of the petrochemical industry, is a critical feedstock influencing polypropylene trade dynamics. Furthermore, derivatives like Styrene Butadiene Rubber (SBR) and Acrylonitrile Butadiene Styrene (ABS) are also integral to the regional market. Trade insights and verified B2B platforms help manufacturers and suppliers build strong networks while enhancing transparency in pricing and quality standards. Aritral offers AI-driven solutions for international trade, simplifying communication between stakeholders in the polypropylene sector. With tools like global sales assistance and AI-powered marketing, it enables smoother transactions and better visibility in the Southwest Asia polypropylene sale market.
-
Styrene Butadiene Rubber: Trade Dynamics in West Asia & Middle East
Styrene Butadiene Rubber (SBR) is a key petrochemical product driving trade dynamics in West Asia and the Middle East. SBR, a synthetic rubber derived from butadiene and styrene, is widely used in industries such as automotive, construction, and footwear. The Middle East has positioned itself as a significant hub for SBR production and export, leveraging its abundant petrochemical resources, including butane, propane, and ethylene. Verified exporters and importers on Middle East trade platforms facilitate the exchange of SBR and related petrochemicals, ensuring streamlined supply chain solutions across Asia. West Asia’s SBR market benefits from increasing demand in Asian markets, particularly in countries like India and China, which are major consumers of automotive tires—the largest industry reliant on SBR. Polypropylene and ethylene also play pivotal roles in shaping trade dynamics in the region, with polypropylene serving as a complementary product in packaging and textiles. Trade advertising platforms in the Middle East enable businesses to gain actionable market insights and promote SBR alongside related commodities like Acrylonitrile Butadiene Styrene (ABS), resin, nylon, and polybutadiene. Advancements in logistics and verified B2B marketplaces in Asia have streamlined the transportation and storage of SBR.
General specifications of SBR highlight its superior abrasion resistance, durability, and cost-effectiveness compared to natural rubber, making it a preferred choice for manufacturers. However, challenges such as temperature sensitivity during storage and transportation require precise supply chain solutions. Aritral, an AI-driven B2B platform, simplifies the buying and selling of SBR and other petrochemicals across West Asia and the Middle East. By offering verified regional product listings and enabling direct communication between businesses, Aritral enhances business networking and global sales assistance for exporters and importers. Its AI-powered marketing tools ensure that trade opportunities for products like SBR are maximized in competitive markets.
-
Resin Trade Dynamics in Middle East & Asia: Market Insights
The resin market in West Asia and the Middle East is a dynamic hub for global petrochemical trade, driven by diverse product demand and strong regional production capabilities. Resins such as polypropylene, polybutadiene, and nylon, along with specialty products like phenolic, alkyd, silicone, and epoxy resins, play crucial roles in industrial applications ranging from packaging to automotive manufacturing. The Middle East, with its abundant ethylene production, serves as a key supplier of resin derivatives, shaping trade dynamics across Asia. Ethylene, a vital petrochemical feedstock, is widely utilized for producing polyethylene and other derivatives, making it a cornerstone of Middle Eastern exports. Verified B2B platforms have enhanced the efficiency of ethylene trade by providing market insights and connecting reliable exporters and importers. Polypropylene, another major resin, has witnessed increasing demand in Asian markets due to its versatility and cost-effectiveness. Middle Eastern producers capitalizing on their petrochemical infrastructure have made the region a significant export hub for polypropylene. Similarly, the trade of styrene butadiene rubber (SBR) and acrylonitrile butadiene styrene (ABS) has grown steadily, with B2B marketplaces playing a pivotal role in facilitating transactions, providing supply chain solutions, and promoting verified listings.
Specialty resins such as polyester, phenolic, alkyd, and epoxy resins are also integral to the Middle Eastern export portfolio, catering to industries like construction, electronics, and coatings. The demand for nylon, propelled by industrial applications, is another growing segment in the regional market. Additionally, butane and propane, critical for LPG production, further underscore the region"s petrochemical prominence. Platforms like Aritral simplify the complexities of resin trade by enabling direct communication, offering product listings, and delivering AI-driven marketing solutions. These tools empower businesses to navigate the resin market effectively while leveraging Middle Eastern supply chain strengths and export opportunities. "
-
Application of ABS polymer in plastic injection
ABS polymer is widely utilized in the automotive sector for injection-molded components, including interior and exterior parts like dashboard panels and bumper covers. Its applications extend to electronic enclosures, consumer goods, and various household items due to its moldability and aesthetic appeal. The affordability of ABS makes it a preferred choice in the plastic injection industry. Additionally, ABS"s structural diversity allows for various properties, enabling manufacturers to create products with different shapes and uses. The polymer is also employed in appliance components, toys, recreational products, and certain medical devices due to its durability, impact resistance, and chemical resistance. Innovations such as MBS alloy have emerged to enhance ABS"s properties, offering alternatives with high transparency but lower tensile strength. Overall, ABS remains a versatile material in plastic injection molding across multiple industries.
-
Which of Asian petrochemicals produces ABS polymer?
Asia"s abundant reserves of acrylonitrile, butadiene, and styrene make it a prime location for ABS polymer production. Countries like South Korea, Taiwan, and Japan have advanced petrochemical industries supported by significant investments in infrastructure and technology. Major producers such as LG Chem, Chi Mei Corporation, and Formosa Plastics Corporation leverage their proximity to raw materials and major markets to reduce costs and enhance delivery efficiency. The region"s favorable policies promote growth in the petrochemical sector, further boosting ABS production capabilities. In the Middle East, companies like Tabriz Petrochemical and Ghaed-Basir Petrochemical also contribute to ABS manufacturing. The demand for ABS is rising due to rapid industrialization across Asia, with applications spanning automotive, electronics, and construction sectors. Competitive pricing is achieved through lower labor costs and efficient supply chain management. However, challenges such as recycling contamination need addressing to maintain quality in recycled ABS products.
-
What are the uses of ABS plastic in the industry?
ABS plastic is valued for its mechanical properties, including toughness, impact resistance, and rigidity, making it ideal for various industrial applications. Its thermal stability allows it to maintain performance under temperature fluctuations, while its chemical resistance enables use in environments with exposure to acids and oils. ABS is widely utilized in the automotive sector for components like dashboards and bumpers due to its durability and moldability. In consumer electronics, it serves as a material for housings and connectors. Additionally, ABS is popular in 3D printing for creating prototypes and functional parts. Despite some disadvantages such as flame sensitivity and opacity, these can be mitigated through alloying with other materials. The ease of processing ABS through methods like injection molding enhances its appeal across industries, including household appliances and construction. Its versatility allows customization to meet specific application needs.
-
What is Acrylonitrile Butadiene Styrene?
Acrylonitrile Butadiene Styrene (ABS) is a widely used thermoplastic polymer known for its toughness, impact resistance, and dimensional stability. Composed of acrylonitrile, butadiene, and styrene, ABS combines the strengths of these monomers to create a versatile material suitable for various industries. Its properties include chemical resistance, heat resistance, and hardness from acrylonitrile; impact resistance from butadiene; and rigidity from styrene. ABS is prevalent in consumer electronics like keyboards and phone cases, as well as in automotive parts, household appliances, and construction materials. The polymer"s machinability allows for precise component production through conventional methods such as cutting and drilling. ABS is also cost-effective compared to other engineering thermoplastics and offers good electrical insulation properties. However, it may not be suitable for all applications due to its limited chemical resistance and potential degradation under prolonged sunlight or high temperatures. Therefore, careful consideration of application requirements is essential when selecting ABS. "
-
Advantages and disadvantages of using ABS polymer in plastic injection
ABS polymer offers significant advantages for plastic injection molding, including excellent impact resistance, ease of processing, and good flow properties. Its versatility allows for modifications to enhance specific characteristics, making it suitable for various applications. ABS provides a smooth surface finish, reducing the need for additional finishing processes. It also exhibits good chemical resistance, making it ideal for environments where contact with different substances is common. However, ABS has notable disadvantages such as a low melting point, which limits its use in high-temperature applications like medical implants. Its resistance to corrosion and UV rays is also low, leading to potential degradation over time when exposed to sunlight or harsh conditions. Additionally, ABS can warp during cooling and has moderate shrinkage that requires careful design considerations during production. Despite these drawbacks, the material"s ductility and affordability contribute to its popularity in producing everyday plastic products. "