Middle East Cement Consumption
Cement is a material that has the ability to stick sand particles to each other and is used in making concrete or mortar. Cement depending on its type is used in making concrete counterparts, cement blocks, in mass and hot weather concreting, building foundation, walling ,tiling, curb , utility pole, anti-sulfation, and many other applications. The human need for cement and concrete to create infrastructure and improve living standards has always existed from the past to the present time, passing of time will be a way to step in the field of using advanced cement. The world cement industry will undergo changes that will ultimately result in reduced energy consumption, reduced clinker use, reduced carbon dioxide emissions and the use of automation systems and information technology.
Advances in the cement industry will lead to the production of cements with higher strength and durability along with cost-effective and energy efficiency. China is the major producer of cement. India is the next major producer after china and Vietnam is placed in the third position, United States, Egypt, Indonesia and Turkey are ranked fourth to seventh main producers of cement in the world. Cement is transferred in two form from factory to the consumers; bagged and bulk form. Bagged form t is loaded by especial cement transporting machine. Cement should be stored in dry environment. In this case cement can be stored for a longer period of time. Bagged cement should be free of lumps. Bulk cement can be used three month if storage favorable conditions rules observed.
What is cement?
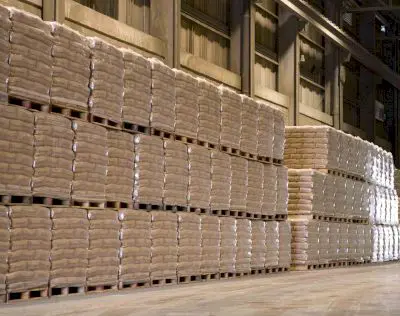
Cement is a Building Materials that has the ability to stick sand particles to each other and is one of the most widely used materials in the construction industry by creating a solid and integrated body of particles as well as making concrete or mortar. Cement is made of a combination of calcareous materials, clay, silica and mineral oxides at a temperature of 1400 to 1500 degrees Celsius. Cement is a chemical product that hardens in combination with water and the resulting product is durable and resistant to moisture. Cement is one of the most widely used materials in road and dam construction and generally in construction field. Cement usually is used as an adhesive mortar in all stages of construction works.
During hydration, the cement paste reacts with water, forming chemical compounds that create a network of interlocking crystals. This process contributes to the hardening and setting of the cement, resulting in a solid and strong material. The hardened cement provides structural stability to buildings, bridges, roads, dams, and various other construction projects. It's important to note that cement is different from concrete. Cement is an ingredient used in the production of concrete, which also includes aggregates (such as sand and gravel) and water. When cement is mixed with water and aggregates, it undergoes hydration and hardening, forming the solid material known as concrete.
What is cement?, Read More ...
Add your import and export orders to this list
Warning: Undefined variable $formTitle in /home/anbar/domains/anbar.asia/anbar/inc/html/desktop/orderform.php on line 10
Warning: Undefined variable $marketName in /home/anbar/domains/anbar.asia/anbar/inc/html/desktop/orderform.php on line 12
Warning: Undefined variable $location in /home/anbar/domains/anbar.asia/anbar/inc/html/desktop/orderform.php on line 12
If you want to trade in the , please join in Anbar Asia. Your order will be shown here, so the traders of contact you
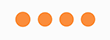
What are the types of cement and what are they used for?

There are several types of cement, each with its own specific characteristics and applications. Ordinary Portland Cement (OPC) is the most widely used cement for general construction purposes. It is suitable for various applications, including residential buildings, commercial structures, bridges, pavements, and most common concrete works. Portland Pozzolana Cement (PPC) PPC is known for its enhanced workability and durability. It is commonly used in hydraulic structures, marine environments, sewage works, and mass concrete constructions. It is also suitable for plastering, masonry, and finishing works.
Environmental factors, such as temperature, humidity, and exposure to aggressive substances, can influence the performance of concrete. Some types of cement are designed to perform better in specific conditions. For instance, low heat cement reduces the heat generated during hydration, making it suitable for massive concrete structures that are prone to thermal cracking. Sulphate resistant cement is suitable for environments where the concrete may come into contact with sulfate-rich soils or water, which can cause deterioration. With growing awareness of sustainability, there is an emphasis on reducing the environmental impact of construction materials. Blended cements, which incorporate supplementary cementitious materials such as fly ash or slag, offer improved sustainability by utilizing industrial by-products and reducing the carbon footprint associated with cement production.
What are the types of cement and what are they used for?, Read More ...
Future of cement industry
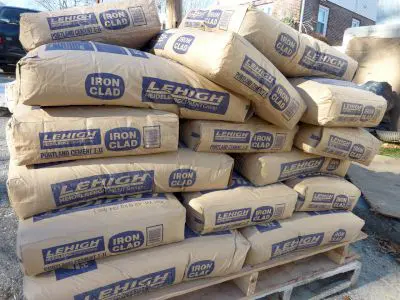
The cement industry is increasingly focusing on reducing its environmental impact. Efforts are being made to develop alternative cementitious materials, such as geopolymers or calcium sulfoaluminate cements, which have lower carbon emissions compared to traditional Portland cement. Additionally, there is a growing emphasis on energy efficiency, use of alternative fuels, and adopting cleaner production technologies. The industry is likely to continue investing in research and innovation to improve sustainability and mitigate environmental concerns. There is a growing interest in utilizing waste materials as alternative raw materials or fuels in cement production. This approach contributes to waste reduction and resource conservation. Industrial by-products like fly ash, slag, and rice husk ash are already being used as supplementary cementitious materials, and this trend is expected to continue. The development of advanced technologies to convert various waste streams into valuable resources for cement production is likely to gain traction.
Continuous advancements in cement production technologies can lead to improved efficiency, reduced energy consumption, and lower emissions. Emerging technologies, such as carbon capture and utilization/storage (CCU/CCS), novel kiln designs, and alternative calcination processes, have the potential to revolutionize cement manufacturing. These technologies aim to minimize carbon dioxide emissions, enhance energy recovery, and increase the use of renewable energy sources. The cement industry is embracing digitalization and automation to optimize production processes, improve quality control, and enhance operational efficiency. Data analytics, artificial intelligence, and machine learning are being leveraged to optimize raw material blending, process monitoring, predictive maintenance, and energy management. Digital tools and automation can help reduce costs, increase productivity, and ensure consistent product quality.
Future of cement industry, Read More ...
What changes will occur in the cement industry in the future?

The cement industry will continue to prioritize sustainability and environmental stewardship. Efforts will be made to reduce carbon emissions, optimize energy consumption, and minimize the environmental impact of cement production. This may involve adopting alternative cementitious materials, implementing carbon capture and storage/utilization technologies, and utilizing renewable energy sources. The use of alternative cementitious materials, such as fly ash, slag, and pozzolanic materials, will likely increase. These materials can partially replace traditional Portland cement, reducing the carbon footprint of concrete production and promoting waste utilization. Blended cements, incorporating supplementary cementitious materials, are expected to become more common.
Changes in the design of separators, cyclones, fans, and burners can help optimize the control of exhaust gases in cement production. Efficient gas cleaning systems, including electrostatic precipitators and bag filters, can be employed to reduce particulate emissions and improve air quality. The cement industry is increasingly embracing digital technologies and automation systems to optimize production processes, improve quality control, and enhance operational efficiency. Data analysis, real-time monitoring, and predictive maintenance driven by big data and artificial intelligence can optimize energy usage, streamline operations, and reduce downtime. However, the implementation of digitalization and automation also raises the importance of ensuring cybersecurity measures to protect manufacturing plants from potential cyber threats.
What changes will occur in the cement industry in the future?, Read More ...
High Tech Cement and Clinker
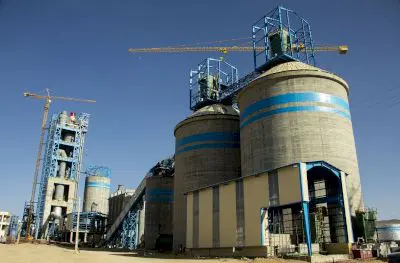
High-tech cement and clinker refer to advanced and innovative materials used in the construction industry that offer improved performance, durability, and sustainability compared to traditional cement and clinker. These materials are developed through technological advancements and research to meet the evolving needs of the construction sector. Blended cements are a type of high-tech cement that incorporate supplementary cementitious materials (SCMs) such as fly ash, slag, silica fume, or limestone. These materials are added to the cement formulation to enhance specific properties such as strength, durability, workability, and sustainability. Blended cements offer improved performance and reduced environmental impact compared to ordinary Portland cement (OPC).
Factors such as overcapacity in a number of countries in the field of cement industry, demographic changes, including an increase in the elderly population in the coming years, changing the situation of developing and developed countries indicate that the demand for cement by the middle of the present century will face a reduction of 30 to 60 percent. With the development of many developing countries, projects around the world will move towards modernization and reconstruction. In the meantime, considering the possible conditions, a number of cement factories in the world will disappear in history or will have to change their application.
High Tech Cement and Clinker, Read More ...
The world's top cement producers

LafargeHolcim is the largest cement producer globally, formed by the merger of Lafarge and Holcim in 2015. It operates in over 70 countries and has a strong presence in Europe, North America, and emerging markets. CNBM is a state-owned enterprise in China and is one of the largest cement producers in the world. It has a wide range of subsidiaries involved in cement production, building materials, engineering services, and more. Anhui Conch Cement is a major cement producer based in China. It has a significant market share in China and has expanded its operations internationally. Anhui Conch Cement is known for its focus on innovation and sustainable development.
Buzzi Unicem is an Italian company with operations in several countries, including the United States, Germany, Italy, and Mexico. It focuses on the production and distribution of cement, ready-mix concrete, and aggregates. UltraTech Cement is the largest cement manufacturer in India and a subsidiary of the Aditya Birla Group. It has a significant presence in India, the UAE, Bangladesh, and several other countries. Dangote Cement is a Nigerian multinational cement manufacturer. It is the largest cement producer in Africa and has operations in several countries, including Nigeria, Ghana, Zambia, Tanzania, and Ethiopia. Votorantim Cimentos is a Brazilian company with a strong presence in Latin America. It operates in various countries, including Brazil, Argentina, Bolivia, and Peru, and is one of the largest cement producers in the region.
The world's top cement producers, Read More ...
Loading cement for consumption and cement warehouse
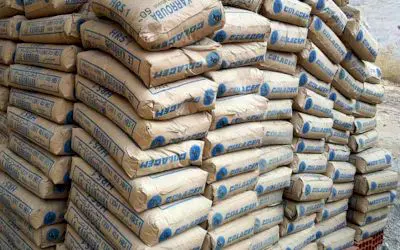
Loading cement for consumption and operating a cement warehouse involves the process of receiving bulk or bagged cement from the cement manufacturer and storing it in a facility for distribution and sale. Bulk cement is typically transported in specialized tanker trucks or railcars. At the cement manufacturing facility or a designated loading terminal, the bulk cement is loaded into the tanker trucks or railcars using pneumatic or mechanical loading systems. These systems transfer the cement from storage silos or containers to the transportation vehicles. The design of a cement warehouse should consider factors such as storage capacity, accessibility, ventilation, and safety regulations. The warehouse layout may include racking systems, storage bays, and designated areas for different types of cement. Adequate space should be allocated for maneuvering vehicles and equipment.
Efficient inventory management is crucial for maintaining stock levels and ensuring timely availability of cement for customers. This involves tracking incoming shipments, monitoring stock levels, and implementing a first-in-first-out (FIFO) system to ensure older stocks are used first. Inventory management systems or software can be employed to streamline these processes. Proper quality control measures should be in place to ensure that the stored cement meets the required standards. This may involve regularly inspecting the cement for quality, conducting tests, and monitoring the storage conditions to prevent moisture ingress or contamination.
Loading cement for consumption and cement warehouse, Read More ...
Precautions in cement storage

To ensure the quality and integrity of cement during storage, several precautions should be taken. Cement should be stored in a dry environment to prevent moisture absorption, which can lead to clumping and reduced quality. The storage area should be well-ventilated to maintain proper air circulation and prevent the buildup of humidity. Avoid storing cement in areas prone to leaks or condensation. Cement bags or bulk cement should be protected from direct contact with moisture. Store cement off the ground on pallets or racks to prevent moisture absorption from the floor. If storing bags, ensure they are stacked in a manner that allows air circulation and minimizes contact with walls or floors. Consider covering bulk cement or using moisture barriers if necessary.
Ensure that the storage area is secure and access is restricted to authorized personnel. This helps prevent theft, tampering, or unauthorized handling of the cement. Implement security measures such as surveillance cameras, locks, and appropriate access controls. Periodically inspect the stored cement for any signs of moisture, clumping, or deterioration. Check bags for damage or signs of pests. Promptly address any issues to prevent further damage or quality degradation. Provide training to personnel involved in cement storage on proper handling, storage guidelines, and safety precautions. Emphasize the use of personal protective equipment (PPE) when handling cement, such as gloves and dust masks, to protect against potential health hazards.
Precautions in cement storage, Read More ...
Where is the first destination of Middle East cement exports?

The GCC countries, including Saudi Arabia, the United Arab Emirates, Qatar, Kuwait, Oman, and Bahrain, are major consumers and importers of cement from the Middle East. These countries have experienced significant construction and infrastructure development, creating a high demand for cement. Several North African countries, such as Egypt, Algeria, and Tunisia, have been prominent destinations for cement exports from the Middle East. These countries have seen substantial construction activities and infrastructure projects, leading to a demand for cement imports. Some East African countries, including Kenya, Tanzania, and Sudan, have imported cement from the Middle East. These regions have witnessed rapid urbanization and infrastructure development, driving the demand for cement imports.
The UAE is one of the largest cement exporting countries in the Middle East. It has a strong cement industry and exports cement to various markets, including neighboring countries and regions. Although Turkey is geographically located at the crossroads of Europe and Asia, it is often considered part of West Asia (Middle East) in terms of its cultural and economic ties. Turkey has a significant cement industry and is known for exporting cement to various countries, including those in the Middle East. Iran has a substantial cement industry and is among the largest cement producers in the world. It exports cement to several countries in the Middle East and beyond.
Where is the first destination of Middle East cement exports?, Read More ...